Boron as an element is by no means a major contributor to the Earth’s mass. This is somewhat surprising given the variety of uses boron possesses and how it plays an important role in some of today’s most vital operationsand economies. The applications of boron in organic chemistry are really impressive and it is beyond the scope of this publication to cover them in detail. However, some of them are worth highlighting to demonstrate the significance of this element in many diverse fields.
Importantly, while boron maintains some characteristics with its neighbors on the periodic table (carbon and silicon), it is chemically distinct, and this distinction is what enables its broad utility. Over many years chemists took advantage of boron’s chemical usefulness and many new applications involving its use have been developed. Boron, since its isolation in 1808, has continued to be a popular subject of study. The discovery of pyrophoric triethylborane by Frankland in 1859 marks the beginning of the chemistry of organoboron compounds. Triethylborane is known to be readily oxidized in air to diethylborinic acid; and further by a second, much slower oxidation step, to a more stable and crystalline ethylboronic acid. This sequence is the first known synthesis of boronic acids. The next major advance in boron chemistry dates back to 1926 when borazine (known as “inorganic benzene”) was synthesized for the first time by Stock and Pohland. Many new developments in boron-based reagents came from work during the World War II due to increased interest in using diborane in vaporizing uranium. This era marks the discovery of two contrasting reducing agents (NaBH4 and LiBH4) as well. A breakthrough for boron’s advancement was the discovery of hydroboration of alkenes by H. C. Brown in the mid 1950’s. His work has increased the level of interest in organoboron compounds and their applications. Tri-coordinate organoboron compounds have proven to be an important class of molecules as they can be used not only in synthetic applications but also as advanced materials, for example in Organic Light Emitting Devices. Boron binds easily with halogens (with the exception of iodine) to form an important class of compounds as well. The heavier the halogen the more aggressive the Lewis acid is. On the other hand, the more ionic character of the boron-halogen bond, the less stable bond. Naturally occurring boron comprises of two isotopes (the 11B 80.22% and 10B 19.78%). The 10B isotope has a high neutron absorption cross section that is exploited in nuclear reactors to control neutron flux. When 10B captures a neutron, a nuclear reaction occurs 10B(n,a)7Li ejecting an alpha particle. This characteristic has been exploited in Boron Neutron Capture Therapy (BNCT), an area of active research for boron chemists for several decades, for treatments of a variety of aggressive cancers, often those found in the brain.
When one thinks about the utility of boron, the Suzuki-Miyaura cross coupling reaction typically comes to mind. It is a very valuable synthetic reaction that was developed in late 1970’s and because it wasn’t patented is nowadays one of the most common carbon-carbon bond forming methods in organic synthesis. The Suzuki-Miyaura reaction brought boronic acids and esters, the main reaction precursors, into the spotlight. From the 1970s onward the demand for boronic acids has increased dramatically ultimately driving the development of new, more economically feasible synthetic methods and applications for both their preparation and their uses. Low molecular weight boronic acids have found many diverse applications due to their electronic and physicochemical properties as well. They have been developed as enzyme inhibitors, drug carriers and sugar sensing agents.
Standard routes for the preparation of boronic acids involve utilization of Grignard- or lithiated reagents with trialkyl borates. Frequently, commercially available reagents such as: trimethyl borate or triisopropyl borate have been exploited in this reaction. Although most boronic acids are crystalline solids and can be handled in the presence of air or moisture, they are prone to dehydration and formation of oligomeric anhydrides such as the trimeric boroxines. The organoboronic acid esters (boronates), on the other hand, are less polar and easier to handle due to the hydroxyl groups being masked. The ester moiety serves as a protecting group which at the same time alleviates the reactivity of the boron-carbon bond. The bulkier the ester moiety the more stable the molecule is. Therefore the cyclic esters such as pinacol have been recently utilized in many applications. The most common way to prepare boronates is by reaction of the pre-isolated boronic acid with the alcohols or diols (Scheme 1).

Scheme 1 Synthesis of Aryl Boronates
There also exists a possibility to transesterify smaller dialkyl esters like a methyl ester with bulkier alcohols or 1,2-diols. Usually cyclic boronates are prepared from the more air-sensitive or less stable boronic acids and 1,2-diols, such as catechol or pinacol, as they exhibit slower rates of proto-deboronation when compared to the corresponding boronic acids. An alternative route, though often more expensive, involves transition metal catalysis with appropriate tetraalkoxydiboron or dialkoxyborane reagents such as bis(pinacolato)diboron or the corresponding pinacolborane. These reagents are presently commercially available which accounts for their applications being prevalent in the literature. There is a new trend to use newly commercially available cyclic borates (Scheme 2) such as dioxaborinanes (six-member ring framework) and dioxaborolanes (five-member ring framework) with Grignard- or lithiated reagents for the synthesis of their corresponding organoboronates. The reaction does not require cryogenic conditions and proceeds well even on larger scales.

Scheme 2 Cyclic Organoborates
More stable than cyclic organoboronates are the organotrifluoroborate salts. This class of organoboron compounds has utility due to high carbon-boron bond stability towards oxidation, protodeboronation and nucleophilic attack. The ease of their preparation, purification and long- term storage makes them valuable reagents in organic synthesis. In addition to Suzuki-Miyaura coupling, potassium organotrifluoroborates participate in a variety of other useful reactions including: 1,2- and 1,4-addition, C—O and C—N bond formation, halogenation and allylation reactions.
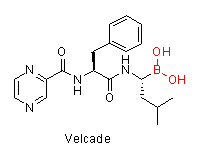
Increasing attention in boron chemistry has been invigorated by the recent US FDA approval of a boron-containing peptidic proteosome inhibitor, bortezomib (Velcade), indicated for multiple myeloma and mantle cell lymphoma. Bortezomib contains a boronic acid moiety which is crucial to its mechanism of action. The interest of exploring boron containing therapeutics is also driven by the unique electronic properties of boron, which allow it to act as a transition-state mimetic for the tetrahedral intermediate of peptide bond cleavage observed in proteolytic enzymes. Currently several other boron-containing molecules are in the preclinical and clinical stages of development to treat multiple disease conditions, such as inflammation, diabetes and cancer. For example, the benzoxaboroles, a class of compounds wherein the boron atom is incorporated into a heteroaromatic ring system, have provided a number of interesting anti-inflammatory, antifungal and antibacterial properties according to recent research. So why do we not have more boron-containing drugs? The main reasons for it are: boron toxicity that was initially incorrectly believed to be very high among many medicinal researchers coupled to not having enough synthetic tools to introduce the boron into the molecules. The recent development of many new synthetic methodologies allows medicinal chemists to more easily design drug-like boron containing molecules and explore their properties. Furthermore, as research shows on the Velcade example, the toxicity of the boron-containing molecule does not come from boron itself but from the drug’s mechanism of action. There is overwhelming data for the safety of boron. Boric acid has a LD50 of 2660 mg/kg (rat, oral) which is almost as high as regular table salt at 3000 mg/kg (rat, oral). Boron is found in fruits, vegetables and it is considered an essential plant nutrient. Boric acid is used in eye wash solution and many creams as well. It would rather plainly appear that the human body knows how to safely and effectively deal with boron. So the question to focus on now is not what happens to boron in the human body but what happens to the rest of the drug’s molecule when the boron is cleaved off and where does the entire molecule also interact while boron is intact, much like any other typical drug candidate.
Relative to other elements like carbon, nitrogen, hydrogen or oxygen, the chemistry community is still in a process of exploring the benefits of boron in many different fields. As mentioned above, the unique properties of boron (chemical, physical and biological) offer an interesting opportunity to investigate new areas of application. Moreover, environmentally friendly and relatively inexpensive raw materials incorporating boron can be easily utilized to build high value product. Feel free to contact us today to explore how you can begin utilizing organoboron compounds in your chemical endeavors to further amplify your business efforts!